© Copyright 1996, Dr. Charles S. Tritt
with the heat released maintaining the temperature of the carbon bed. If the carbon becomes too cold, the reactions will not proceed at an appreciable rate.
The carbon in the above reaction could be coke or charcoal derived from coal or wood, respectively. Coke and charcoal is made by heating the starting material in the absence of oxygen. This process could be carried out in the same apparatus as the water gas reaction described above. A complex mixture of volatile chemicals is released during the formation of coke and charcoal. This mixture contains water vapor, liquid hydrocarbons vapors, gaseous hydrocarbons (like methane, ethane and propane), vaporized “tars” and some hydrogen. The condensable fraction of this vapor could be used as a liquid fuel (like naphtha or white gas). The tar could be used sealing, waterproofing, etc.
Separating the hydrogen from the carbon monoxide (CO) and carbon dioxide (CO
2) could be done using a permeation process. Permeation exploits the differences in the rates at which different gases penetrate certain membranes. In a lowtech society, the membrane could be woven fabric, paper, large leaves or animal membranes. The membranes would be coated or saturated with tar, liquid fuel or animal or vegetable fats (or a combination of these) to obtain a differential permeability to hydrogen and the carbonaous gases. As you can imagine, the resulting membranes would be quite flammable.
The permeation process might have to be carried out in multiple stages to obtain the desired hydrogen purity in the final gas. Each stage would process less gas but increase the purity of the product as shown in the following table for a hypothetical process:
Volume Entering (cubic meters) |
Volume Vented (cubic meters) |
Volume of Product (cubic meters) |
Purity of Product (% hydrogen) |
1000 | 900 | 100 | 50.0 |
100 | 90 | 10 | 75.0 |
10 | 9 | 1 | 87.5 |
1 | 0.9 | 0.1 | 93.8 |
A fraction of the product entering each stage would have to be vented in order to achieve the concentration of hydrogen in the product. This is an inevitable aspect of this type of process. Bellows might have to be used between the stages to move and repressurize the gas.
Process Operation
The discussion below refers to the following figure.
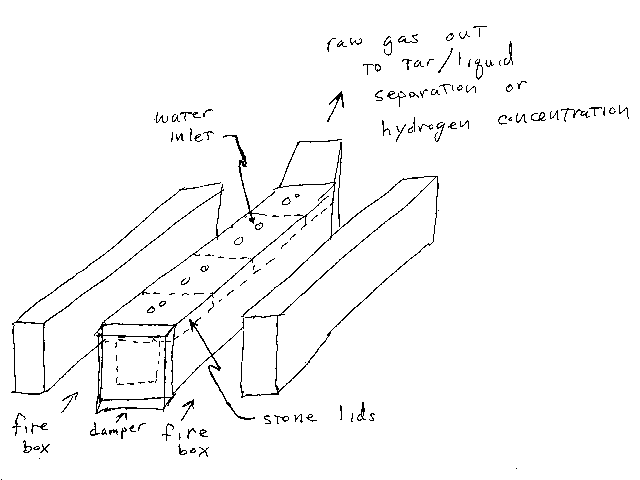
Making the coke or charcoal.
- Load the roasting box with coal or wood (respectively).
- Close the damper to keep oxygen out.
- Build and maintain large fires in the fire boxes.
- Wait.
- Collect the flue gases in the tar/liquid fuel recovery system (really a condenser) if desired. Otherwise, just vent them to the atmosphere (there would be no EPA to object).
- When the flue gas flow rate drops off, the coke or charcoal is ready.
Making the Water gas.
- Maintain the fires in the fire boxes.
- Start admitting water into the water inlets (ports) of the reactor.
- Open the damper slightly to keep the temperature of the carbon up. Process operation would be pretty tricky. The operator would need a lot of experience gained by trialanderror and therefore would be very valuable. Too much oxygen would reduce yield and make purification more difficult. Too little oxygen would result in the carbon getting too cold and the reaction stopping completely.
- Collect and purify the water gas.
- When the water gas flow rate drops off, let the fires in the fire boxes go out, let the reactor cool, open it up and clean out the ash, repeat the whole process.
Operating the hydrogen concentration and tar/liquid fuel systems would be relatively easy. Once the hydrogen concentration system was setup gas could be pumped into it almost indefinitely and would be separated. The tar/liquid fuel separator would have to be shutdown at intervals to clean the tar out.
Other Notes and Comments
The stone in the water gas reactor would have to be heat resistant (it could not be sandstone, limestone, marble or any other soft, water retaining stone).
The carbon monoxide in the water gas would make it very toxic. Any leaking gas could overcome and kill the workers. Carbon monoxide and hydrogen are odorless so the workers might not notice the problem until it was too late. A high concentration of carbon dioxide in the air makes people breath hard, but in the water gas process described above workers would probably be killed by the carbon monoxide before noticing the effect of the carbon dioxide.
Hydrogen gas is highly explosive when mixed with air over a wide range of concentrations (from 5 to 94%). Both carbon monoxide and hydrogen are flammable. Any event resulting in air mixing with the water gas or purified hydrogen would probably result in a fire or explosion.
Hydrogen tends to leak out of containers. Most materials are at least somewhat permeable to hydrogen so any balloons inflated with it would probably have to be refilled every few days or weeks. They could also be destroyed by shooting flaming arrows into them (nonincinerary projectiles might not would not cause fire, but would cause leaks).
The vapors from the coke and charcoal making operations are carcinogenic and would probably result in the workers and their families getting cancer after ten to twenty years.